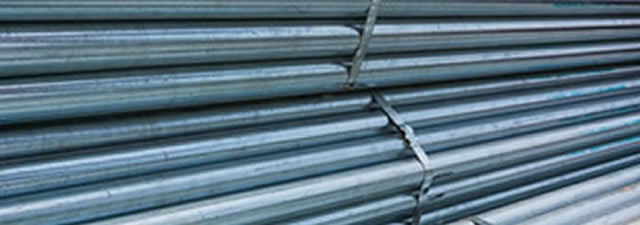
INSPECTION AND SORTING
OF PARTS
We take care of verifying that the products are in compliance with the technical
documentation (plans, specifications, standards, legal provisions, etc.).
We have the necessary means of measurement and testing to check the products.
We assign the product a Quality Note in accordance with the degree of conformity with the specifications.
-
Reception inspections.
With this service we guarantee that the raw materials, components, sub-assemblies that enter the plant and that are used in the production process, meet the established requirements, carrying out:
-
Quantitative Control:
Ensuring that the quantities received correspond to the documentation, counting the pieces and / or weighing them.
-
Qualitative Control:
Ensuring that the quality of the materials received, meets the dimensional and functionality specifications.
This control seeks to guarantee the final quality of the product from the initial quality of the components.
-
-
Batch inspections.
In order to examine and measure the quality characteristics of a product, as well as the components and materials with which it is made, or of a specific service or process; we perform the inspection service following the guidelines of the ISO 17020 Standard.
-
100% Inspection.
-
Attribute sampling inspection.
-
Inspection by sampling by variables.
-
-
Factory inspections.
In order to ensure that the manufacturer meets the specifications of its products, we provide a factory inspection service.
This inspection can occur during:-
The pre production lap.
-
During production lap.
-
At the end of production lap, prior to packaging.
-
During loading lap.
-